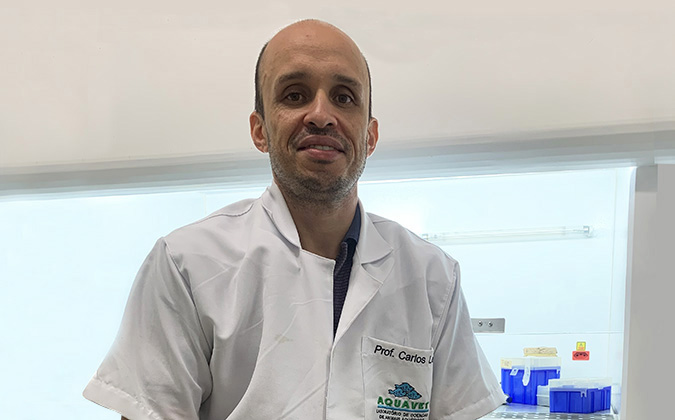
Automatic vaccination in tilapia farming: a new era is coming
By Carlos AG Leal, Professor of Immunology and Fish Health, Veterinary School, Federal University of Minas Gerais-UFMG, Brazil
The use of vaccines in commercial tilapia farming has grown significantly in the last decade, mainly in countries that produce larger fish (over 700 g) for fillet production. Cultivation cycles for these larger fish are longer (6 months to 1 year, according to the region and season), so the fish are more exposed to pathogens in the growing phase, with bacteria of the genus Streptococcus the most prominent.
In this context, Brazil is the country that has stood out the most. According to Professor Ganesh Kumar of Mississippi State University in the USA, only 5% of tilapia produced in the world are currently vaccinated,1 with 40% of that total in Latin America. Data from animal-health companies suggests that Brazil is responsible for 50% of tilapia vaccines used in the region; thus, one in every five tilapia vaccinated in the world is vaccinated in that country.
The first commercial vaccine for use in tilapia in Brazil was registered in 2011: a product to prevent infection by Streptococcus agalactiae serotype Ib. In little more than a decade, vaccines managed to overcome the initial skepticism of producers and become essential products for the industry today.
These immunobiological products began to be widely used from 2015, and it is estimated that more than 250 million doses had been marketed in Brazil by the end of 2022. The efficiency and economic viability of vaccination is increasingly being recognized by the industry, as well as demonstrated by scientific works.
One of the most telling studies, published in 2019,2 evaluated streptococcosis vaccination programs in caged-tilapia farms, showing that for every U$ 0.20 invested by the producer (vaccine + antibiotics + labor + vaccination) they would have an added return of U$ 0.25 — that is, more than 100% return on investment.
Manual methods have flaws
Initially, vaccination programs were carried out in a very rudimentary way on farms. The fish were captured in the tanks, anesthetized in drums with a eugenol solution as an anesthetic and later directed to the vaccination tables. Here, the fish were manually contained and vaccinated intraperitoneally.
Using this type of process, while performance has been satisfactory, there were many instances where levels were below the recommendation of 95% of fish successfully vaccinated.
Each vaccinator was able to vaccinate 3,000 to 5,000 fish per day. In addition to the vaccinators, an extra employee was needed to collect and anesthetize the fish. As the classification of the fish was visual and the tables used for vaccination were not ergonomic, the performance of vaccination and classification throughout the day would decline, leading to these lower rates of coverage. Additionally, in this type of vaccination, counting the number of vaccinated fish is performed by each vaccinator by pulling the trigger of the manual vaccination gun, which results in human error.
Enter the machines
In 2017, new technology started to become available for use in the vaccination process. Vaccination continued to be manual, but the equipment classified the fish before reaching the vaccinators, and after immunization, the fish were counted automatically. Because they were specifically designed for this purpose, these devices have better ergonomics, allowing more comfort for vaccinators and better daily performance.
With the use of this equipment, there was an increase in the daily rate of vaccination in companies, which increased to 5,000 to 10,000 fish per vaccinator per day, with the top figures in the case of very well-trained teams. In addition, the problems of inaccuracy in counting the fish were significantly diminished. However, in many situations, problems with the vaccination rate persisted: despite the technological improvements, the classification system did not reduce the need for labor in vaccination.
For large companies, this constituted a bottleneck for vaccination programs. Each vaccination team — with three vaccinators, one assistant and an average of 7,500 juveniles vaccinated per day over 22 days per month — had the capacity to vaccinate approximately 500,000 juveniles every month. Big tilapia companies with a monthly population of 800,000 to 900,000 juveniles needed at least two vaccination teams. In more extreme cases, such as juvenile producers vaccinating 2 million to 2.5 million animals a month, four or five vaccination teams were required. This need for manpower became a problem for companies.
Technological transformation
In 2021, however, this scenario began to change drastically in Brazil with the introduction of the first semi-automatic tilapia-vaccination machine. Produced and made available to customers by PHARMAQ Fishteq (part of Zoetis), the NFT-20 vaccination machine also brought with it PHARMAQ’s significant experience in the production of equipment for automatic immunization of salmon. All in all, this represented a new and much-needed innovation to tilapia vaccination in Brazil.
Being semi-automatic, the equipment requires manual placement of the fish into cups on a conveyer belt, but the process requires no further human input after that point. It individually scans the fish and determines the animal’s length as well as vaccination site and needle penetration pressure to avoid trauma and injuries in organs adjacent to the injection point. Then after vaccination, the equipment directs the animal to the destination tank according to its length.
With a vaccination capacity of 8,500 fish per hour, the equipment significantly increased the vaccination capacity of large companies. It became possible for a team of three people to vaccinate up to 1.3 million tilapia per month, reducing the required workforce by more than 60% when compared to manual vaccination. Furthermore, its use helps avoid the problems of vaccination rates below the recommended level, as the equipment maintains the same performance throughout the operation, unlike human vaccinators, who tend to tire and reduce the performance and accuracy of vaccination.
There are still no data on the technical-economic performance of using the NFT-20 in Brazil. However, technicians and producers who have been using the machine have anecdotally reported meaningful improvements in the vaccination process and efficiency.
These positive results, combined with the subsequent introduction of another manufacturer’s device into the market, have accelerated the adoption of tilapia-vaccination equipment in Brazil. The use of machines and the reduction in labor involved in the vaccination process should increasingly allow the adoption of vaccination programs right across the Brazilian industry, making the use of vaccines a fundamental pillar for the full development of modern tilapia farming.
1 Kumar G, 2023, personal communication.
2 Delphino MKVC, Barone RSC, Leal CAG, Figueiredo HCP, Gardner IA, Gonçalves VSP. Economic appraisal of vaccination against Streptoccocus agalactiae in Nile tilapia farms in Brazil. Prev Vet Med. 2019;162:131-135.
Posted on: April 04, 2023