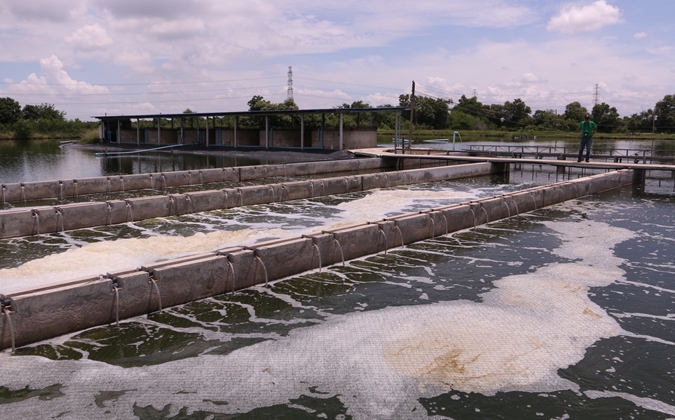
US-born aquaculture system has the potential to transform Thai fish farming
An innovative system initially designed to help US catfish farmers is offering a lifeline to fish producers across Southeast Asia who are facing increased pressure to farm more sustainably.
The In-Pond Raceway System (IPRS), which transforms a traditional earthen pond into a more controlled, high-density production zone, was designed in the United States to intensify production while addressing environmental concerns. Though it never truly took off in its home country, IPRS is now making waves in Asia, where producers are facing calls to increase efficiency and manage disease whilst reducing their environmental impact.
“In the US, IPRS didn’t see widespread adoption due to the nature of our ponds; they’re often too deep or irregularly shaped,” explained Lukas Manomaitis, Senior Technical Advisor for Aquaculture at the U.S. Soybean Export Council (USSEC).
“But in China and now Thailand and Vietnam, where pond areas are shrinking and environmental regulations are getting tighter, the system makes a lot more sense.”
Thailand produces about 1 million tonnes of aquaculture products annually, split roughly 50/50 between freshwater and marine species, with tilapia, Asian seabass, freshwater prawn and shrimp such as Penaeus vannamei and monodon forming the backbone of production. However, rising costs, water quality issues, and limited land availability are pushing farmers to adopt new methods.
“Thailand used to be number one in fishing boat numbers, but there were labour issues and resource constraints,” Manomaitis said. “Aquaculture is still growing every year, but financially, things are getting tighter.”
Intensifying production sustainably
This is where IPRS has the potential to change things.
“You’re taking about 2% of the pond area and converting it into a raceway, a sort of floating pen structure with a concrete base and walls,” explained Manomaitis, who has seen Thailand install six IPRS units so far, used for seabass and tilapia.
“The fish are separated into cells, the water is aerated, and forced to circulate using a baffle wall, which improves mixing and oxygen distribution.”
Each raceway cell holds around 25 tonnes of fish, with water constantly moving to simulate a river-like environment. Solid waste is mechanically removed and sent to sedimentation and oxygenation tanks, where it decomposes. Water is recirculated back into the pond, with only evaporation leading to losses.
“The waste management aspect is a game-changer,” Manomaitis said. “Fish waste is rich in phosphorus, and if that ends up in the environment, it causes eutrophication.
“With IPRS, we can isolate and even reuse those nutrients, for example, in aquaponics or row crop fertiliser, or even producing non-fed species like mussels and oysters, which gives producers another income stream.”
This closed-loop approach is especially critical in a region where water conservation is becoming a strategic priority. According to USSEC data, IPRS can deliver up to three times the productivity of a conventional pond using the same water volume, while also improving feed conversion ratios and fish health.
“Another huge advantage is that unlike traditional pond systems, which typically need to be drained every six months to manage waste and sediment, an IPRS pond can operate for up to five years without being drained,”Manomaitis added. “That’s a big deal in terms of water use and labour.”
Currently, IPRS is primarily used in freshwater production, but trials are underway to adapt the system for marine and brackish water aquaculture.
“There are only a handful of marine systems at the moment because we need to address issues of corrosion and dealing with salt water,” said Manomaitis. “Salt is very hard on the infrastructure, so we need components that can handle that environment.”
In Manomaitis’ experience, the system also improves the quality of the final product. “In tilapia, the meat quality is better because they have to swim against the water current. It’s like they’re going to the gym,” he said. “And because everything is concentrated, it’s much easier to manage feeding, harvesting, and monitoring.”
IPRS also allows for partial harvesting and multi-species culture – a practical benefit in a market where demand can fluctuate. “Producers can stock cells at different times and sizes, so we don’t flood the market all at once,” said Manomaitis. “That helps us manage cash flow and reduce risk.”
Still, there are barriers, and the system isn’t for everyone, he added. “You need reliable electricity 24/7, a good water source, skilled labour, and crucially, access to markets. I’ve had to dissuade people from adopting it unless they can prove they have those pieces in place.”
The system, which costs around $100,000 (about 3.5–4 million Thai baht) to install, typically pays for itself in 3–5 years depending on efficiency. But it requires more than just capital, it needs a strategic approach.
“If you suddenly triple your production, you need three times the fingerlings,” said Manomaitis. “Do you have a reliable hatchery? Can you sell that much fish? These are the questions we ask before supporting implementation.”
Supporting producers to improve production
USSEC works with local producers not just to promote US soy in aquafeeds, but to offer technical services, training, and access to data.
“We’re not a marketing organisation,” Manomaitis said. “We help farmers understand how to use products better, and we support them through the whole value chain – from breeding stock to final sale.”
The IPRS complements USSEC’s sustainability goals, he added. Verified U.S. soy, through programs like U.S. Soy Sustainability Assurance Protocol (SSAP), plays a role in reducing overfishing and diversifying protein sources in aquafeed.
“Soy shines in grow-out diets. It adds essential protein and allows farmers to reduce dependence on fishmeal, which is both costly and environmentally problematic,” he said.
With over 14,000 IPRS units already operating globally, mostly in China, the system is expanding into Southeast Asia, with pilot projects in northern Vietnam and growing interest in Indonesia and the Philippines. In Thailand, it’s still early days, but its potential is clear.
“Then first IPRS system run in Thailand produced 25,000 kilograms of tilapia,” Manomaitis said. “The farmer couldn’t sell it all at once, which showed that production is only half the story. You need to plan your market too.”
Manomaitis is optimistic but pragmatic. “It’s an elegant system, but it’s not a magic bullet. For the right producers, it can be transformative. But you’ve got to do your homework.”
Watch the video:
Posted on: May 19, 2025